1. СТЕКЛОПЛАСТИКОВОЕ КАТЕРОСТРОЕНИЕ XXI ВЕКА |
После года выпуска пробной продукции завод в Литтл-Фолз (шт. Миннесота), освоивший технологию формования стеклопластиковых корпусов VEC, в июле 2000 г. вышел на полную мощность. Эта технология обещает революцию в области малого судостроения.
По существу то, о чем идет речь, похоже на литье под давлением. Каждую из двух половинок литейной формы, разогретых горячей водой, покрывают тонким слоем напыляемого гелькоута, затем раскатывают в ней слой стеклоткани (внешний слой будущего сэндвича), вырезанной точно в размер. В “нижнюю” половину формы раскладывают формообразующие вкладыши из жесткого пенополиуретана. Накрывают нижнюю половину формы верхней и в образовавшуюся полость между слоями стеклоткани подают образующую средний слой-заполнитель патентованную жидкую смесь на базе смолы и катализатора. За 25 минут происходит полная полимеризация, и жесткую “цельнолитую” заготовку формуемой конструкции можно вынимать. За одну минуту облой (затвердевшие подтеки) удаляется на станке с ЧПУ, и заготовка поступает на монтаж оборудования и сборку.
Впрочем, сложности есть, как и в любом новом деле. Секрет технологии VEC (Virtual Engineering Composites) в автоматизированном дистанционном управлении. Датчики в литейных формах контролируют более чем 500 переменных показателей, определяющих температуру, вязкость, текучесть, массовую плотность, высыхание геля и пиковые экзотермы. Эти текущие данные постоянно поступают в компьютер, расположенный в сотне миль — в штаб-квартире VEC Technology в Гринвиле (шт. Пенсильвания), который и управляет производственным процессом. Производство может управляться из любой точки мира компьютером, подключенным к сети Интернет.
VEC — детище Джина Кайрила, которое приобрел Ирвин Джейкобс, владелец крупнейшей компании катеростроительного холдинга “Genmar” в Миннеаполисе*.
Проект потребовал немалых инвестиций (30 млн. долл.). Джейкобс признает, что он сильно рисковал, делая ставку на VEC, однако он убежден, что это — будущее стеклопластикового корпусостроения.
Надежность продукции, а также быстрота и внешняя простота производственного процесса — безусловно, главные преимущества VEC, в сравнении с традиционными стеклопластиковыми технологиями. На первой очереди завода VEC-1 по новому методу менее чем за год выпущено 1000 катеров “Glastron-185” и “Larson-190”. При этом максимальное зарегистрированное отклонение веса заготовки корпуса от нормы составило 1 фунт (0.454 кг).
Толщина трехслойного сэндвича точно соответствует чертежу. Внешний вид отлитой конструкции заслуживает самой высокой оценки. Корпуса получаются более жесткими и менее подверженными вибрации и шуму на ходу. Процесс требует всего 35 минут в сравнении с минимум 8 часами при обычной технологии. Кроме того, здесь проще вносить мелкие изменения: иногда для этого достаточно просто поменять внутренние пенополиуретановые формообразующие вкладыши.
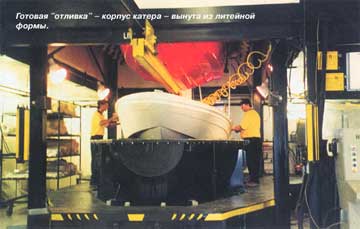
Цех VEC-1, насчитывающий 45 человек, за 10 месяцев выпустил первую партию 19-футовых корпусов. Весь завод в Литтл-Фолз насчитывает 850 человек и выпускает в год 4000 моделей “Glastron” и 4500 моделей “Larson” длиной от 17 до 33 футов
Еще одно ключевое отличие технологии VEC от традиционной — чистота. Атмосфера в цеху почти совсем лишена всепроникающего запаха стирола, столь характерного для обычного стеклопластикового производства. Поскольку испарения стирола уже ограничиваются в Европе экологическими нормативами, ясно, что это — немаловажное преимущество новой технологии. По словам разработчиков, усовершенствованная система VEC-2 снижает испарения стирола на рабочем месте на 90%. Но и совершенствование VEC-2 не прекращается. “Мы не останавливаемся ни на минуту и никогда не удовлетворяемся достигнутым. VEC-3 сейчас развертывается в Питтсбурге”, — говорит Джейкобс. Там загрязнения воздуха будут сведены к нулю, тогда производство можно будет развернуть прямо в Лос-Анджелесе.
А пока на заводе в Литтл-Фолз в новом здании площадью 8990 м2, построенном в начале 2000 г., работают две литейные установки VEC и один из самых мощных в мире сборочно-отделочных конвейеров. С того момента, как отлитая заготовка будет вынута из формы при помощи пневматических присосок, до момента поступления готового катера на склад все операции механизированы. Это сборочный конвейер в традициях Генри Форда, перенесенный в 21-й век. Корпуса перемещаются по цеху при помощи цепей, утопленных в пол, а элементы оборудования катера опускаются сверху. Органы управления всеми этими операциями подвешены на оптимальной с точки зрения эргономики высоте.
Хотя новый завод работает, полной мощности он еще не достиг. Скоро будут добавлены еще две литейные установки, и тогда предприятие выйдет на плановую производительность 10 000 корпусов в год (т.е. сможет выпускать по одному корпусу каждые 22 минуты).
Первоначально завод будет выпускать восемь моделей “Glastron” и “Larson” 2001-го года длиной от 17 до 21 фута. В течение трех лет на технологию VEC будут переведены все модели длиной до 24 футов, хотя технически вполне возможен выпуск и более крупных корпусов. Тем не менее, Джейкобс говорит: “Катера уже освоенных размерений — это 85% нашего рынка. Для начала надо справиться хотя бы с этим”.
Этой зимой “Genmar” планирует внедрить новую технологию VEC на заводе “Wellcraft” в Сарасоте (шт. Флорида) и затем, в течение следующего года, на заводе по выпуску басс-ботов “Ranger” в Арканзасе.
“До последнего времени катеростроительная индустрия пребывала в 19-м веке. Мы перенесли ее сразу в 21-й век”, — так считает руководство “Genmar”.
Сторонние обозреватели согласны с такой оценкой. Патриция Муди и Ричард Морли в своей книге “Машина технологии”, опубликованной в начале 1999 года и дающей прогноз развития производственных технологий до 2020 года, включили систему VEC в пятерку самых важных изобретений под номером три. Интернет в этом списке занимает только пятое место.
2. ТОЧНОСТЬ ПРЕВЫШЕ ВСЕГО |
При любом варианте технологии стеклопластикового судостроения процесс постройки корпуса состоит из трех последовательно выполняемых операций: 1 — изготовления форм для формования по ним технологической оснастки (матриц, пуансонов-болванов); 2 — изготовления самой оснастки; 3 — собственно изготовления секций корпуса в этой оснастке. Высокая точность необходима на всех стадиях, причем обеспечение полного соответствия сложной пространственной формы крупногабаритного изделия — корпуса — теоретическому чертежу судна обычно представляет большую сложность.
Тем большую сложность представляет изготовление форм для получения термопластовых корпусов и литейных форм, рассчитанных на получение тонкостенных корпусов малого судна. Добиться требуемой точности при использовании традиционных для судостроения снимаемых с плаза шаблонов и лекал очень трудно, поэтому автоматизация переноса форм с чертежа на материал давно представлялась первостепенной важности делом.
В городе Чезапик (шт. Вирджиния) двое сыновей знаменитого кораблестроителя и конструктора Дональда Блаунта решили эту задачу. Уильям и Даг в конце 1999 г. учредили компанию “Precision Shapes of Virginia” (PSOV). Прежде чем нанять 32 рабочих, которые сейчас вручную доводят литейные формы до совершенства, братья выписали из шведской компании “ABB Automation” робот и подключили к нему программное обеспечение от “RTS Networks” (Финляндия).
Шведский гигант-киборг может создавать любые формы длиной до 80 футов с такой точностью, что в любой пространственной точке отклонение от проектных размеров не будет превышать один миллиметр. Это означает и повышение качества изготовления корпуса и ускорение производства и выпуск значительно более широкого ассортимента моделей.
“Хорошая яхта начинается с точных и жестких форм, и это — наш конек”, — считают братья Блаунты. Сегодня они получают две трети дохода от производства матриц для формования и одну треть — от выпуска литейных форм, но в будущем выйдут на первый план именно литейные формы.
Как и во всяком проекте, все начинается с кульмана. Конструкторы при помощи программы автоматизированного проектирования создают приблизительный чертеж, после чего начинается процесс согласования деталей между Блаунтами и заказчиками — представителями верфи. Эта игра в пинг-понг может длиться недели. Наконец, когда клиент утвердит цифровые чертежи и обводов, и общего расположения судна, электронное проектирование заканчивается и начинается физическое создание судна. В действие вступает робот — две его гигантские механические руки начинают выфрезеровывать матрицу из блоков пенопласта, склеенных в единый массив. Из проекта робот получает данные о форме корпуса, преобразованные в специальные команды — где, что и сколько резать: манипуляторы приводятся в движение и “высекают” из пенопластового айсберга скульптуру будущего корпуса. Каждая “рука” может двигаться вокруг семи осей (тогда как у большинства ныне существующих роботов — только вокруг пяти) и режет пенопласт со скоростью 0.9 м в секунду. После удаления пыли и стружки из бесформенной массы предстает будущий корпус катера: вот пространство для рыбного садка, там — люк для спуска в машинное отделение; репортерам демонстрировалась матрица для изготовления нижней части формы, предназначенной для отливки секции палубы.
Робот специально вырезает матрицу с солидным минусовым допуском порядка четверти дюйма. По окончании этого этапа рабочие напыляют на матрицу слой смолы толщиной три четверти дюйма. Затем тот же робот другим, более точным веретенообразным инструментом снимает лишнее до точных размеров, то есть с допуском 1 мм. Поскольку в смоле нет армирующего стекломатериала, инструмент практически не стачивается. Этот этап длится на 20% дольше, чем этап грубой обработки заготовки, поскольку робот добивается идеальной точности формы. Однако поскольку процесс полностью автоматизирован, робот трудится круглые сутки.
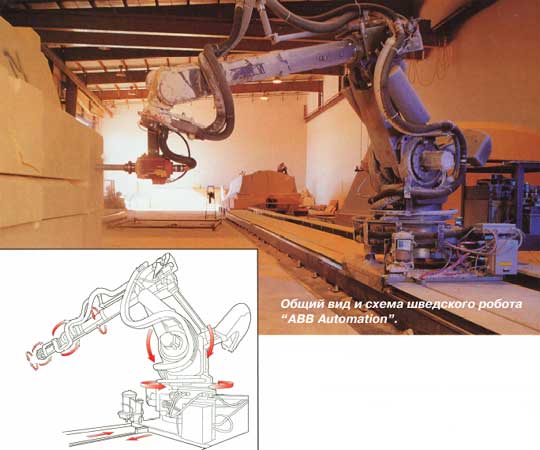
“Поскольку манипуляторы движутся по направляющим длиной 80 футов, которые расположены по обе стороны от ДП, мы можем запустить в работу одновременно три или четыре формы, — объясняет Даг журналистам. — Мы просто оставляем робота на ночь, а наутро находим три или четыре заготовки, готовые для дальнейшей обработки”.
На этом обязанности робота кончаются и начинаются заботы людей. Они переносят формы в другую часть цеха и укрепляют их массивными стальными распорками, чтобы не допустить коробления при обработке поверхности. Первым накладывается слой грунтовки на основе дюратека (Duratec), затем наносится специальная грунтовка, поддающаяся обработке наждачной бумагой тонкостью 600 единиц; после этого накладывается последний слой черного глянца, который зачищается бумагой тонкостью 1000 или даже 2000 единиц. Нанесение и обработка этих покрытий занимает около трех недель.
После этого можно готовить вторые половинки литейной формы с учетом необходимой толщины пространства между ними. Для этого иногда на ту же матрицу сначала наносят слой оранжевого геля. Следом наносится слой смолы из полиэстера с толченым стеклом, а в последнюю очередь — слой стеклопластика для придания прочности. Рабочие снимают заготовку и укрепляют ее на металлической основе, чтобы предотвратить изменение формы.
Большую экономию, особенно при выпуске малосерийной продукции, дает использование так называемых "плавающих форм". Вместо того, чтобы делать обе половины литейной формы абсолютно жесткими, применяя мощные металлические подкрепления, используют принцип несжимаемости воды: их накрывают камерами, заполняемыми водой. Давление воды снаружи, воспринимающее давление литейной смеси изнутри формы, препятствует ее деформации.
Вот и все. Спустя пять недель после утверждения проекта корпусостроитель получает комплект литейных форм, идеально соответствующих цифровой модели корпуса. Заказчик может не бояться: отверстия под крепеж соединения секций палубы и корпуса совпадут, никаких отклонений обводов, снижающих ходкость судна, не будет.
Многие корпусостроители теперь могут перейти на полузаказную форму обслуживания клиентов. Поскольку PSOV готовит новые формы быстрее, чем раньше, строители могут выпускать несколько моделей по одному проекту, что снижает расходы и время. Большее количество проектов — это более широкий ассортимент, который смогут предложить дилеры покупателям. Например, на существующий проект ничего не стоит добавить верхний мостик.
3. НОВОЕ В ПОСТРОЙКЕ КОРПУСОВ ИЗ ЛЕГКИХ СПЛАВОВ |
![]() |
Первая стадия постройки корпуса по процессу Hydra-Core DH: на выставленный набор укладываются и привариваются тонкие листы наружного слоя сэндвича. |
Ныне строители алюминиевых яхт начинают вторгаться в область, где до сих пор безраздельно господствовал стеклопластик. Используя новейшую патентованную технологию, основанная в 1995 г. американская фирма “Hy-Lite Powerboats” строит скоростные спортивные катера из алюминия, что дало этой верфи новый импульс развития.
По иронии судьбы, данная технология подразумевает такую же трехслойную структуру конструкций корпуса, что и в самых высокотехнологичных корпусах из стеклопластика.
Главное преимущество трехслойной стеклопластиковой конструкции хорошо известно. Легкий заполнитель пространства между наружной и внутренней скорлупами увеличивает жесткость и прочность корпуса, по сравнению с вариантом из сплошного стеклопластика, одновременно снижая его вес. Примерно те же преимущества обеспечивает и новая технология — два тонких слоя алюминия с пенопластом между ними оказываются выгоднее со всех точек зрения.
В традиционном варианте стеклопластикового корпуса средний слой является неотъемлемой составной частью конструкции, поскольку приклеивается к наружной и внутренней скорлупам в ходе ее изготовления. Однако в данном случае дело обстоит уже не так.
Обычно один толстый слой обшивки при традиционном процессе постройки корпуса из легкого сплава приваривается к набору и из-за высокого нагрева возникают большие температурные деформации, которые потом приходится устранять рихтовкой и нанесением эпоксидных покрытий. Это — трудоемкий процесс, к тому же добавляющий изрядную долю веса и увеличивающий стоимость. Именно из-за проблем со сваркой и необходимостью гибки относительно толстых листов алюминия он и уступил место стеклопластику, где может быть получен корпус сколь угодно сложной формы при условии изготовления комплекта дорогостоящей оснастки.
Десять лет назад три брата Фрейсена — Генри, Джон и Джейк — переориентировали свою компанию TUG Weld Manufacturing на выпуск скоростных судов (до этого она выпускала грузовые суда из стали и алюминия для Великих Озер). Они пришли к убеждению, что алюминий дает много преимуществ, в сравнении со стеклопластиком (прочность, меньший вес, долговечность, трещиностойкость, стойкость к образованию раковин и расслоению), но технологию постройки алюминиевых судов необходимо революционизировать.
Десятилетие опытно-конструкторских работ привело к созданию патентованной технологии Hydra-Core DH, предполагающей использование более легкого (высотой 50 мм) и часто поставленного поперечного набора корпуса и применение гораздо меньших толщин листового материала для упрощения гибки и уменьшения объема наплавляемого при сварке металла. Внешняя и внутренняя обшивки привариваются к набору, причем внутренняя обшивка, имеющая меньшую толщину, чем наружная, приваривается к полке набора только изнутри корпуса. По окончании сварки в образовавшееся пространство шириной 50 мм закачивается в жидком виде пенополиуретан. Этот заполнитель — средний слой — обеспечивает необходимую прочность и жесткость конструкции, исключает конденсацию влаги, создает слой теплоизоляции, а также снижает шум и вибрацию. Набор корпуса изготавливается так, чтобы пенопласт свободно распространялся и заполнял все пространство между обшивками. Такая же технология используется при создании реактивных истребителей и космических челноков. Малость шпации, наличие жесткого среднего слоя и уменьшение объема сварки практически исключают возникновение сварочных деформаций.
В 1994 г. новая технология была впервые продемонстрирована при строительстве 39-футового прототипа — катера “Hy-Lite 394”. После его доводки появилась коммерческая версия — 48-футовый “Orion XV” (проект Майкла Петерса из Сарасоты). Корпус с обводами глубокое V имел вентилируемый двойной редан; с двумя 500-сильными моторами “MerCruiser Bulldog V-8s” катер развивал скорость свыше 112 км/ч.
Недавно на “Hy-Lite” была построена 55-футовая моторная яхта “Green Wing I”, которая должна стать самой быстроходной среди дизельных судов своего класса; она оснащена 1400-сильным двигателем “Caterpillar 3412s” с приводом Арнесона. На ходовых испытаниях на озере Окенчоби (Флорида) она легко развила скорость 123 км/ч.
Концепция со всей очевидностью оправдала себя при постройке остроскулых глиссирующих моторных яхт. Строитель судов из стеклопластика в гораздо большей степени привязан к ранее изготовленной (и дорогой) литейной форме, тогда как в данном случае строитель может изготовить корпус почти любой формы по желанию заказчика. Поскольку покупатели становятся все более требовательными и реже бывают довольны стандартными корпусами, фирма “Hy-Lite” надеется на повышенный спрос и готова удовлетворить самый изысканный вкус. И возможность удовлетворять любые требования заказчика может стать весомым аргументом в споре между сторонниками алюминия и стеклопластика.
Н. К.
* История Genmar восходит к 1977 г., когда Ирвин Джейкобс приобрел долю предприятия “Larson Boats”. Вскоре он купил “Lund Boats”, потом еще ряд катеростроительных предприятий. Сегодня эта частная компания выпускает 12 моделей катеров и имеет девять предприятий в шести штатах США и Канаде. Штат — 6400 человек. В 1998 г. холдингом выпущено 38 000 лодок и катеров длиной от 10 до 100 футов. “Genmar” считает себя вторым по объему производства строителем прогулочных катеров в мире. Компании принадлежит 10% всех продаваемых в США моторных судов. Последний финансовый год, закончившийся 30 июня, “Genmar” закончила с суммарным доходом 858 млн. долларов; выручка от продаж составила 61 млн. долларов.